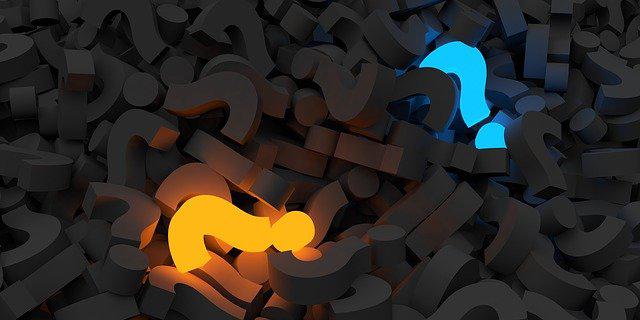
Safety at the workplace is of the utmost importance. Whether the workplace is a quiet office building or a hectic factory, all employees deserve to work in a place that is free from harm. Unfortunately, not all safety hazards are easy to recognize. However, with a workplace safety audit and analysis, those hazards are easy to identify.
When a company is safe, the employees aren’t the only people who benefit. Shareholders benefit from the business being safe, simply because a safe business isn’t busy taking care of the excessive costs related to employee injuries. When the business is safe and employees are happy, customers and investors bring their money and the business succeeds.
With a thorough job safety analysis like the ones conducted at this website, businesses can find where weaknesses exist and injuries could happen. The analysis also finds places where the business is not functioning as efficiently as it can. A job safety analysis proactively looks at how businesses can become less hazardous and more efficient. It is important that the analysis is shared with employees so they can learn how to be safer and more efficient in their daily tasks.
These steps are useful for analysing and auditing workplace hazards:
Decide why the risk analysis is needed
Before a major undertaking like a hazard analysis and audit, there should be a good reason why the steps need to be taken. If someone has been injured on the job, then you have a perfectly good reason to begin the process. But, an injury does not have to be the catalyst. The idea that an injury could happen is a good reason to begin an analysis.
However, it is important to understand if there are actual hazards and risks in the workplace. A workplace risk involves the idea that something harmful could happen to an employee. A hazard is an actual thing that could cause harm. A ladder is an example of a hazard and the risk is not properly training someone to climb the ladder.
Begin with the most dangerous department or job
The best place to start is the department that has the most hazards and risks. You might be able to use actual injury data to determine where to begin, or you might just have to make a decision about what department seems the most hazardous. Usually, the most dangerous departments have to lift heavy things, climb ladders, drive specialized vehicles, work with potentially harmful chemicals, and work with heavy machinery.
Remember, this is only the beginning. Once this department’s analysis is completed, the analyst will move on to the next departments. Eventually, the entire company will be analyzed.
Ask helpful questions
As the job is analyzed, questions need to be asked. They should include questions like:
- What hazardous things are in the area?
- What problems could arise while doing this job?
- What is the likelihood that an accident could occur?
- What else could go wrong?
- What training does the employee need?
- What safety steps need to be implemented?
Break down the job into clear steps
Once the questions have been answered, it’s time to look at the jobs and work out the steps to completing it. These steps should be clear and easy to follow, so if someone has to be replaced on the job, the replacement can do it exactly the same way. Those steps need to be recorded and place somewhere that the employee can find.
The series of steps should be ten or fewer. If there are more than ten steps, then the job becomes jobs and should have defined phases. No matter how unique the business is, many jobs have similar steps, so check out what other businesses do so you do not have to waste time recreating what has already been done. If necessary, include steps that involve putting on safety gear, like goggles or gloves. Before the steps are recorded, the employees who regularly do the jobs should try out the steps to be sure they explain the steps clearly.
Decide how to eliminate or lessen the hazard
While the steps are being created, it is important to look at what hazards can be removed. For example, would it be beneficial to remove anything that could cause an employee to trip and fall? The analysis and audit should look for ways to complete the job that do not need hazardous materials. If the hazard cannot be eliminated, then the analyst should look for ways that the employee can complete the job with less chance for injury.
Determine preventative steps
Since hazardous materials are difficult to completely remove from the workplace, the analyst should be able to offer steps that will prevent injury. Usually, there are four questions that are asked when looking at ways to prevent hazards from being too risky. They include
- Is there a way to remove the hazard from the workplace?
- Is there a way to use safety measures to contain the potential hazard?
- How can the steps of the job be altered to eliminate contact with the hazard?
- What protective equipment can reduce or remove exposure to the hazard?
Once the questions are answered, the steps to complete the job should be reassessed to determine the safest possible way to complete it. The analyst, employees, and stakeholders should look at protective equipment to determine what is the most useful, too.
Record findings and share with employees
As soon as the decisions are made, employees need to be made fully aware of the steps they need to follow to safely do their job. While some employees might find major changes to be disruptive to their day, most will appreciate having a safe and efficient way to do their jobs.
With a strong analysis and audit, the workplace becomes safer for everyone who walks through the doors. Employers who build a culture that believes in safety is a business where people want to come to work. An important part of that culture involves having clear job descriptions with easy-to-read steps for each responsibility. Those steps should be stored in a convenient spot for the appropriate employees to access.