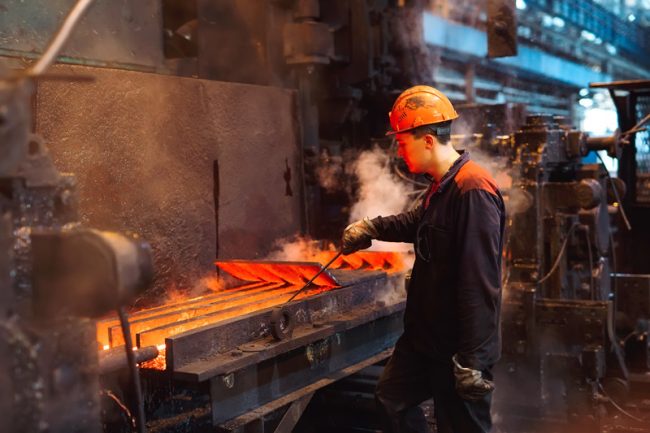
It is for centuries now that human beings have learnt about iron and steel. Steel was the main discovery which played an important part in the industrial revolution and has now emerged as the backbone of the modern economy based on industrialization. A world without steel is hard to imagine. Steel is used for constitution, vehicles, engines, machines everywhere. Iron is an element which is found abundantly in Earth. Even a tiny bit of it is needed in every kinds of construction.
Steel is really a versatile element in every aspect, starting from the composition of it, its properties, the strength to weight ratio and the ability steel holds which makes it recyclable multiple times. These qualities are different from any other material which make steel a popular element. Let’s have a look how steel and iron, the most powerful materials are made.
Steel Manufacturing Process
There are two raw materials which can be used for steel manufacturing. One is hot metal from blast furnace or steel scrap or sometimes both are used. Steel in general terms is actually iron from which most of the carbon is removed, which makes it tough and more ductile. In a steel trading company, steel is generally sold as HR sheet or cold rolled steel. Two mostly used steel making processes are:
Basic-Oxygen Steel Making
The basic raw materials required for this process are hot metal from blast furnace and steel scrap. Oxygen which has very high purity is blown towards the metal at a very high pressure. What the oxygen does is it combines with carbon and other unwanted mixed elements and eradicates them from the molten metal. The carbon vaporizes and leaves as carbon monoxide which can later be collected and reused as fuel. Then the steel is tapped out and made to cool down.
Electric Arc Furnace
The Electric Arc furnace is made up of a circular bath which has movable roofs. Through the roof three graphite electrodes can be raised or lowered whenever needed. Once the steel scraps are put inside the bath, the furnace with electrodes is lowered. A powerful electric current is passed through the furnace which heats the space and melts the scraps. Then oxygen is blown into it and lime and fluorspar are added.
Read here –What Industries Use HR And CR Rolled Sheets And How?
Iron Manufacturing Process
Iron, as you know, is generally prepared in blast furnace. At first a mixture of iron ore and coke is heated enough to form a clinker, also called ‘sinter’, which is rich in iron. The whole process depends on sintering as it lowers the amount of waste and in turn helps in providing efficient raw material which can be helpful for manufacturing iron.
The next step is putting the coke, ore and sinter together on the blast furnace along with limestone. A hot air blast, is then inserted through the nozzle, which is located at the base of the furnace. The air blast is enriched with oxygen. Sometimes even coal or oil is added to increase the heat and reduce the coke requirements. What the blast does is distributes the heat to reach a white-hot intensity. Then the iron ore and sinter get melted and tapped out.
Read here – Difference Between Cold Rolling Steel, Hot Rolled Steel & Cold Forming Of Steel